Ensemble de mélange
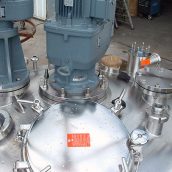
AGIMEL présente pour équiper des REACTEURS de fabrication de produits COSMETIQUES, PHARMACEUTIQUES OU ALIMENTAIRES, un ensemble de mélange équipé d’un Agimélangeur à mouvement contrerotatif, et d’un Agidisperseur à cages colloïdales.
Le mélangeur-malaxeur est composé d’une ancre raclante périphérique, munie de racleurs en Téflon et de pales horizontales, d’une part, et d’une partie centrale constituée d’un arbre équipé de trois étages d’Hélices Tripales ou Bipales Profilées, d’autre part.
L’organe extérieur de mélange crée à la fois un écoulement tangentiel (l’ancre) et un écoulement axial de bas en haut (les pales sur l’ancre).
L’organe central a, quant à lui, un écoulement axial de haut en bas crée par les Hélices Profilées.
Chaque partie du malaxeur est entraînée séparément, par deux motorisations distinctes, équipées chacune d’une variation de vitesse.
La première motorisation pilote l’ancre raclante périphérique, et la seconde dispose d’un arbre d’entraînement traversant, permettant ainsi la rotation simultanée et en sens contraire des deux organes de mélange coaxiaux entre eux.
Des courants de convection ascendants et descendants se contrariant sans se neutraliser, se forment donc dans le produit.
Ce mouvement appelé mouvement contrerotatif, garantit un malaxage parfait même sur des produits difficiles comme les dentifrices, les crèmes cosmétiques ou pharmaceutiques, les mayonnaises, etc…
Le disperseur de fond de cuve est équipé d’une turbine Rotor/Stator à cages colloïdales à très haut taux de cisaillement.
Munie d’une « simple » ou « double » cage Rotor, solidaire(s) d’une hélice de pompage, le tout tournant à l’intérieur d’une cage STATOR, cette turbine soumet le produit, lors de son passage dans la chambre de mélange, à un cisaillement qui permet d’atteindre une granulométrie d’émulsion très poussée (quelques microns).
Un système d’étanchéité par garniture mécanique DOUBLE EFFET équipe cet appareil en standard.
Il est à noter que pour une capacité de réacteur supérieure ou égale à 10000 litres, nous prévoyons deux disperseurs fond de cuve au lieu d’un.
Cela permet de mieux répartir l’effet de dispersion, et surtout de pouvoir adapter les volumes de fabrication selon les besoins, par exemple, fabriquer avec un réacteur 10000 litres, dans les conditions d’un réacteur 5000 litres ou 6000 litres, en ne faisant fonctionner qu’un seul disperseur, sans changer de process.